In my previous blog article, I touched on the impact that cleanliness and debris can have on Fiber optic connecter performance. With this article, I will go over the geometry that helps Fiber achieve the limits needed in today’s Data Center requirements.
Bellcore created a Fiber Optic standard in 1984 and provided this standard for the Telcom Industry until 1997 when it was sold and became Telcordia. Telcordia GR326 CORE has been one of the most recognized standards in the Optics industry for many years. “Regarded as the most complete and rigorous standard for single mode fiber optic connectors. The Telcordia GR-326 standard document sets forth the Telcordia view of the technical generic requirements for, and characteristics required of, connectors used for joining single-mode optical fibers, and for the jumper assemblies made using such connectors”.
In a nutshell, it basically creates a standard that if the manufacturing center meets these parameters, then any fiber will perform as designed when plugged into any supplier that also supports these standards. This is not to say that the Service Life Testing can have a significant impact on the product, but for all intense and purposes, I am going to focus on the geometry side of the process.
Senko Advanced Components did a white paper in 2013 that outlined some of the Service Life Testing and why it can benefit a supplier, you can read that here. I have seen firsthand how hard it can be to be GR326 Certified as I was able to complete the Verizon FOC program in the past. But that is for another day.
Geometry really has several standards, but the most important ones are related to Radius of Curvature (ROC), Apex Offset, Fiber Height, and Angle Polish (APC). Some Technical definitions are as follows.
Radius of Curvature:
The radius of curvature is defined as the radius of the best-fitting sphere over the defined Fitting Area. This can be calculated using a least squares method to find the best radius. Because the Fitting Area is symmetrical around the fiber, the position of the ferrule has no effect on the calculation.
Apex Offset:
Measuring the apex offset (offset of the polish from the fiber) requires defining the “high point” or vertex of the polish. Since the fiber itself could be recessed or protruded, the sphericity of the ferrule surface (as defined by the Fitting Area) is used to calculate the vertex. The apex offset is defined as the distance from the vertex of the ferrule sphere to the center of the fiber. In order to calculate the vertex accurately, the system must be calibrated to determine how perpendicular the ferrule is being held to the reference mirror.
Fiber Height:
Two possible ways to define fiber height are Spherical Height and Planar Height.
- Spherical Height is useful when the ideal connector endface (ferrule and fiber) is considered to be a continuous sphere. It is defined as the difference in height between the center of the fiber and the theoretical height in the center based on the ferrule radius. The Averaging Area is used for both height calculations.
- Planar Height is useful when the ideal connector endface is considered to be a flat fiber in the middle of a spherical ferrule. It is defined as the difference in height between the center of the fiber and the height in the center of the theoretical plane formed by connecting the points on the ferrule at diameter E, the Extracting Area.
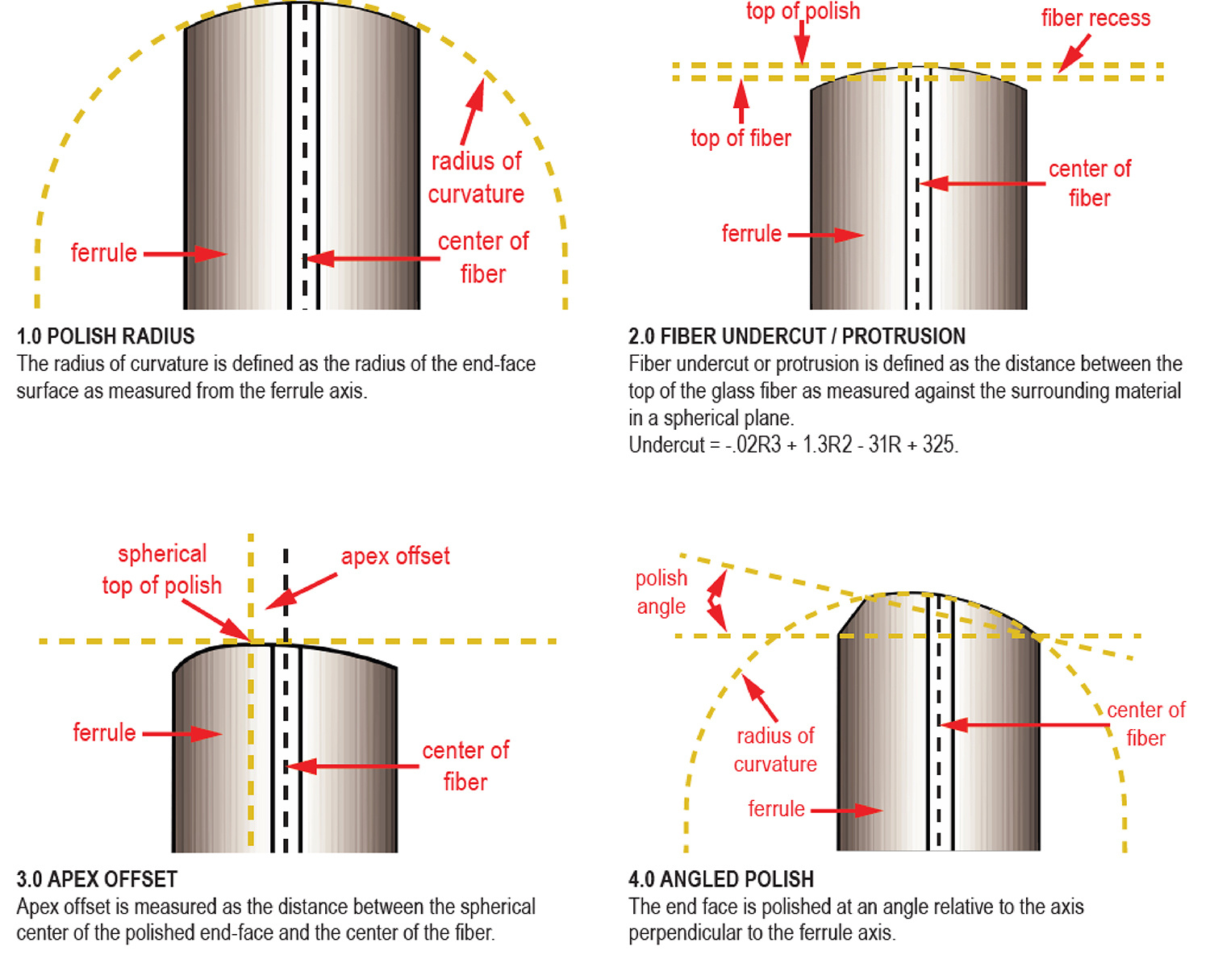
The Table for these specific metrics is defined by the GR 326 Core specification.
Connector Type | Radius of Curvature | Fiber Height | Apex Offset |
UPC | 7-25mm | +50nm to -125nm | <50 um |
APC | 7-12mm | +100nm to _100nm | <50 um |
Fiber Height can vary depending on the Radius of Curvature (ROC) but this should be determined by the Interferometer you are using to measure the connectors.
There are several good Interferometers on the market, but my best experience has been with Direct Optical Research Corporation (DORC) and Norland, which is now Thor Labs. You want to use a unit that is repeatable and has the support you need should anything occur, but that decision is up to you.
These measurements all play an important role in how the connectors talk to each other. Connectors that are outside the metrics can cause some optical performance degradation in the signal. For instance, if you have a connector with an Apex Offset that exceeds the testing standard you may have a signal but if you were to have to hit a lower loss budget for a 400 Gig site that connection could cause your cables to fall outside that budget.
We are seeing an ever-increasing demand for lower loss at every connector connection within the Data Center. Being able to deliver extremely low-loss products is going to be even more important. Having geometry designed into your product is one way of guaranteeing your cables will drive what your customers demand every time.
Fiber height is another measurement that has greatly increased in significance lately. As temperature becomes more of a factor in connector fiber pistoning, it can have a big impact on cable performance. The further a fiber pulls back from the ferrule will create an undercut and Return Loss can be affected if this goes too far. Troy Cummings, our Production Manager, has put in place an excellent polishing process that keeps our connectors well within the GR326 standards. That allows us to focus on having the best optical performance we can get. Our installers have echoed this many times after installing our cables into their Data Center Projects.
Even when looking at Multi Fiber connectors, GR1435 gives you the same type of foundation for the MTP/MPO connector. Measuring 12-24 fibers at a time and assuring they fall within the Connector contact requirements can be hard. But having a good polishing process defined allows you the benefit of achieving results that the customers demand.
Every Multifiber connector we test will have been assured to be following the specification, so this allows us to see if there are problems early on. This reduces rework and connector repair and replacement. Reducing material costs is a key part of our business plan.
These standards are embedded into our testing process so I am very confident when we test a product it is going to have the best results and can support every customer requirement in the market.